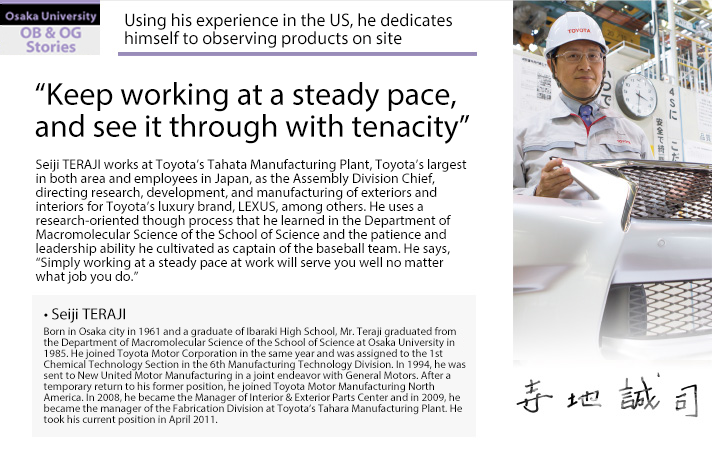
Seiji TERAJI (General Manager, Tahara Plant Final Assembly Division, Toyota Motor Corporation)
Baseball taught him organizational theory
Mr. Teraji began the interview with a smile, saying, “Actually, my son is a 2nd year student at the School of Foreign Studies, so when he went to take his entrance examination, it had been 20 years since I walked through Ishibashi.” His connection with his alma mater continues to this day. There are over 1100 individuals in Toyota’s Osaka University Alumni Association, “Handaikai.”
He started playing baseball while in junior high school, and when he was a second year student at OU, the team won the Kinki Student Baseball Association tournament for the first time in team history. “No matter how hot it got, I put in 4 hours of practice every day in between my studies and research. It was tough, but it worked out in the end.” A skilled second- and third-baseman, he batted cleanup as the 4th spot in the order from his second year. As captain, he got a taste of the difficulty of getting the team to perform like he wanted. “I learned to be patient, and I also got a taste of frustration when the team members didn’t get along and we couldn’t get the results we wanted. But I think that those experiences are alive in my work even today.” The class just below him made it all the way to the Jingu Tournament.
“Just do it”
“In both sports and work, you’re never going to have a perfect record. Even if you’ve got 6 wins to 4 losses, or you win 51-49, a win is still a win. I encourage people at work by saying, ‘I’m not looking for perfection. I’ll take something that’d only get a 4 out of 10, just bring me ten of them.’ Do what you have to do. If it doesn’t work out, move on.”
The topic for his graduation thesis was polyelectrolyte solutions. One of the most fundamental research topics, this topic “actually has nothing to do with my current work at all,” Mr. Teraji laughed. The leader of his study group, Prof. Tadao KODAKA, was a unique individual who would always keep in mind that Mr. Teraji was, in fact, captain of the baseball team, casually sending him off to practice when the time came.
Mr. Teraji wanted to work for a manufacturer. He had an interest in automobiles, and his seniors encouraged him, saying, “If you’re going to go for it, you might as well aim for the top.”
Never put out a defective product
After he entered the company, he started in the resin division. His work in improving technology and putting simulations through trial and error in order to avoid creating defective products had elements of fundamental research and felt rewarding to do, which led him to his work today. Between 1994 and 2004, he was appointed to work in the United States twice for a total of 8 years. Towards the end of his work was right before Toyota overtook GM for the top automobile unit sales in the world. While he was worried that “this would antagonize the US,” he also felt that “it’s these times that require us to get a foothold and come together to get back to basics."
The Japanese take on their tasks diligently, and when something goes wrong, they try to fix it. It’s for this reason that even the smallest details in their work are very clearly designated. But the workers on site in the US don’t quite understand the intent behind this fastidiousness. Mr. Teraji has struggled with directing these individuals in the past.
Driving the company motto home
One of the mottos at Toyota is genchi-genbutsu , or “seeing the actual product on site in person.” Mr. Teraji felt that he should follow through with this motto while in America, so he would head to manufacturing sites and speak with the employees there. “Not everyone has to completely agree with one another, but it’s important to make sure that everyone is headed in a direction that they’ve all agreed upon.” It seems that his experience as captain of the baseball team was useful here as well.
Even in Japan, he sometimes has a difficult time conveying his thoughts to his employees. His superiors urged him on, saying, “Have you told them that 100 times?” This encouragement has stuck with him to this day.
Japanese manufacturing technology is amazing
Japan’s manufacturing industry has long found itself in a predicament due to expansion overseas and catching up to other countries. Even so, explains Mr. Teraji, “Japan’s manufacturing technique and tradition are incredible. We’ll continue to work on the fundamentals in Japan and send that knowhow overseas.” From there, he makes his employees feel a strong sense of pride in being involved in automobile manufacturing. “I’ll keep creating comfortable work sites in order to make high quality, inexpensive products. I can’t just leave everything to the work sites, so I need to absorb and alleviate any dissatisfaction of the managers at those sites. The ability to do this is one of Toyota’s strong points.”
Feelings for Osaka and OU
Mr. Teraji spoke about his alma mater. “I don’t know much about other universities so it’s difficult to compare, but I’m glad I went to OU. I like the intensity of Osaka, and I still record the Yoshimoto New Comedy Troupe on TV. I go to Namba Kagetsu whenever I’ve home as well.” He continued, “Human resources are important. I want OU to portray its vision of the future as both a institute to nurture these human resources and as a world-leading research institute.” Of course, he also keeps up with the baseball standings.
When he was a mid-level employee, he also served as a student recruiter. “If you simply look like you can handle a job on the surface, it’s not going to fly once you’re employed.” To current OU students, Mr. Teraji gave some words of advice, saying, “I want you to show some tenacity in taking on the tasks that you’re given. Young people these days don’t have enough of that. I want you to be free of the fear of failure and show me that you can follow things through to the end.” Mr. Teraji’s fondness for “work sites” and “tenacity” shows a certain tenacity he has for manufacturing.
This is a reprint of the article posted in the Osaka University NewsLetter No. 60 (June 2013).